We offer our clients a personalized experience when we create a custom piece for them, but crafting items for our ready-to-wear gallery involves a different way of thinking about such accouterments. These jewelry pieces are tiny wearable works of art, and crafting such a piece is a gesture that honors what has been made sacred by time and love.
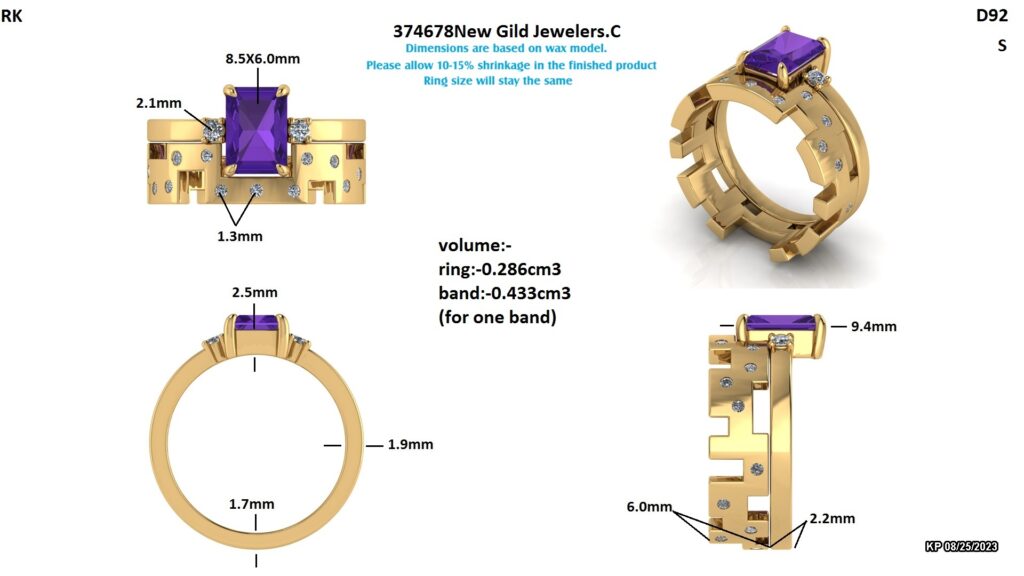
We believe that a well-designed commitment ring or rings celebrate the individual, the union, and the preciousness of love itself. Love is the secret ingredient that shows up in our studio, in our processes, and in our work, and we love sharing how we make the magic happen.
Ready-to-wear pieces begin with the love of a stone. The stone tells us what it wants, as new age as that sounds. This emerald cut, decidedly purple spinel stood out from everything else on the table between me and the gem dealer. Unable to hide my enthusiasm, I snatched up thevstone and put it in the “hard yes” collection of gems for purchase that day.
Meanwhile, an idea has taken hold at New Gild about the creation of commitment ring sets, and that idea was that a wedding band shouldn’t just look good worn alongside an engagement band, but should look good on its own too, because in today’s world a woman will want to leave the bigger rock at home for things like rock climbing (pardon the nuance) and vacations.
Our team has gotten creative with our so-called, “wave bands” that feature a continuous wave all the way around, such that a ring with a prominent center stone would fit up against the band no matter the positioning. But this purple spinel was all straight lines and angles…
I had the word, “gear” on my mind for seemingly unknown reasons (actually it was from watching Silo on AppleTV) and I sketched a band with a rectangular indent to go alongside a solitaire ring featuring the emerald cut stone, but it broke the aforementioned “rule” about a wedding band needing to look good on its own, too. So I sketched the indents in different sizes, depths, and positions everywhere on the band, ensuring that the solitaire could fit flush and into the band in several locations. A sprinkling of small diamonds everywhere would make the set pop, and I added them to the sketch.
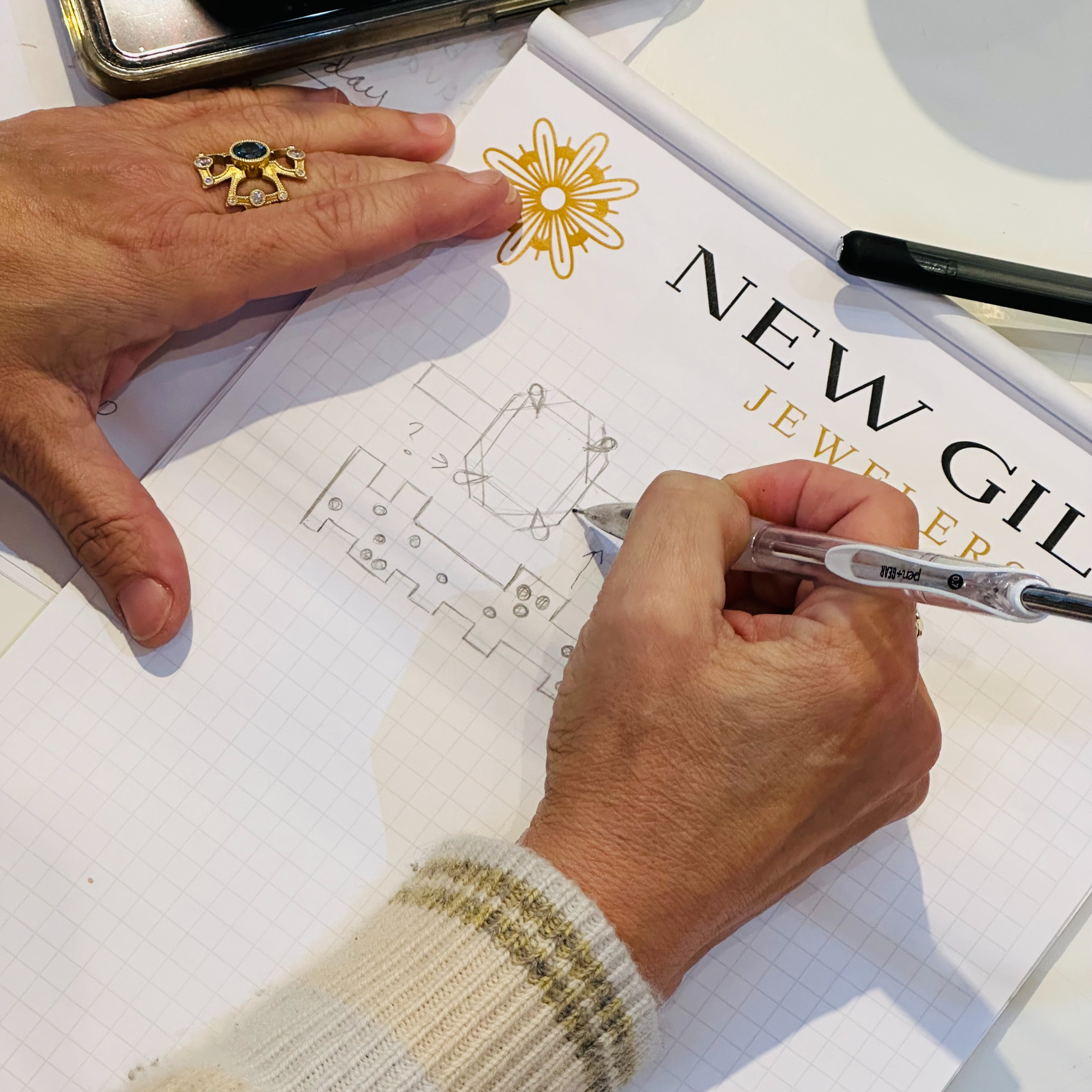
Our team then converted the sketch to CAD imagery, in order to visualize the ring in 3D and troubleshoot any aesthetic or technical challenges. The CAD work is revised until it’s perfect, and then a 3D printer is used to print a wax model of the rings. We use the wax models to examine the feel of the ring in the hand, and to ensure that the stones fit perfectly in what will be their new home.
Using lost wax casting, the wax is converted to gleaming gold! From there, our team polishes the casting, and our master jeweler and co-owner Kelsey sets the stones. The finished ring is named, photographed, and placed in the gallery where it awaits its person. He or she will spot it, love it, and make it their own.
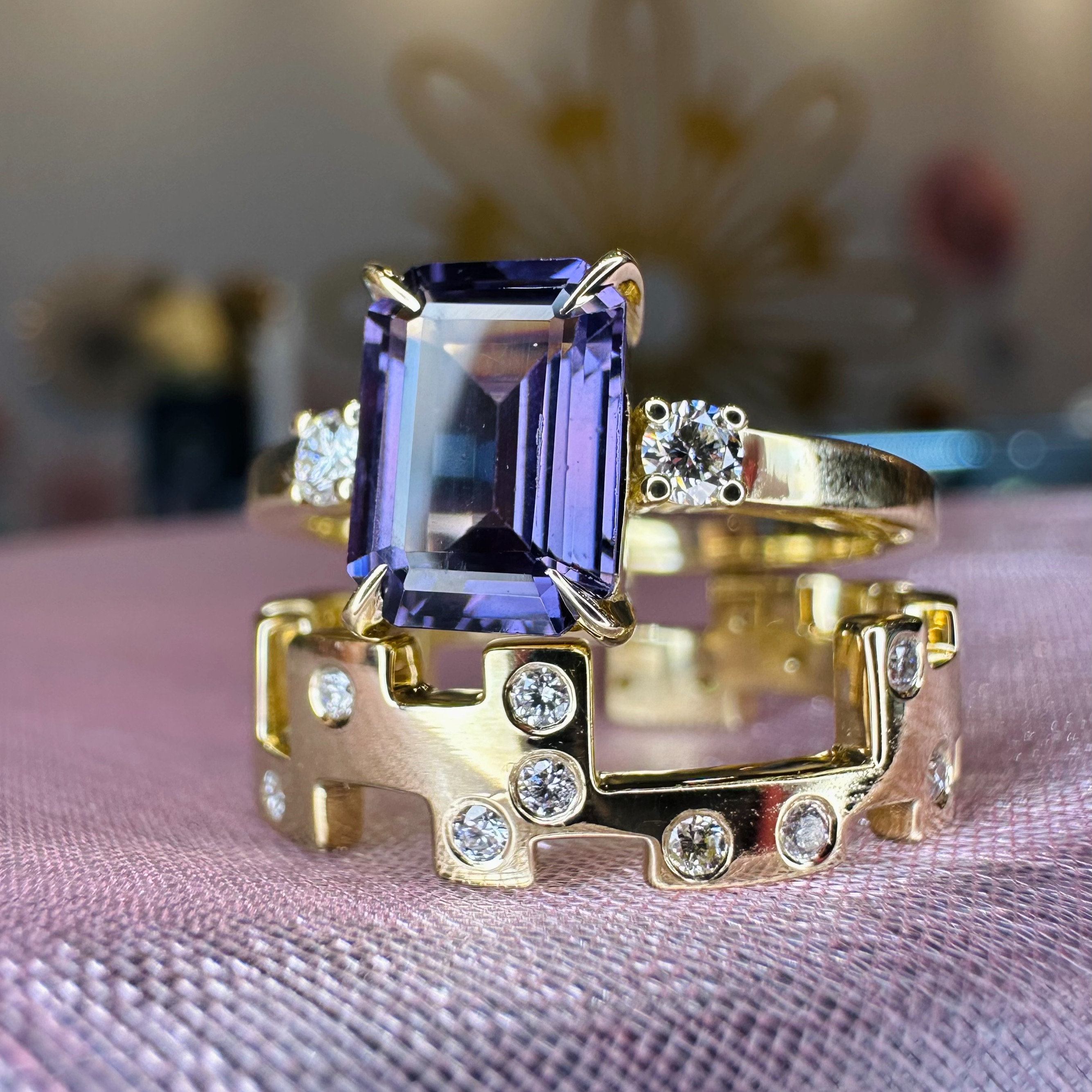
Our greatest ambition is to create work that provides each client with a happily ever after that actually lasts ever after. I always say that when I run into my clients in the produce aisle at Whole Foods in three years, I want them to run up and hug me. Our team has played a small part in many beautiful love stories, and that means everything!